一、项目场景
视觉检测技术在制造业中具有广泛的应用场景,尤其适用于对产品外观、尺寸、形状和缺陷进行高精度检测的环节。这些场景包括但不限于:
汽车制造:检测发动机零件的表面质量、车身外观的划痕和凹陷、零部件的装配精度等。
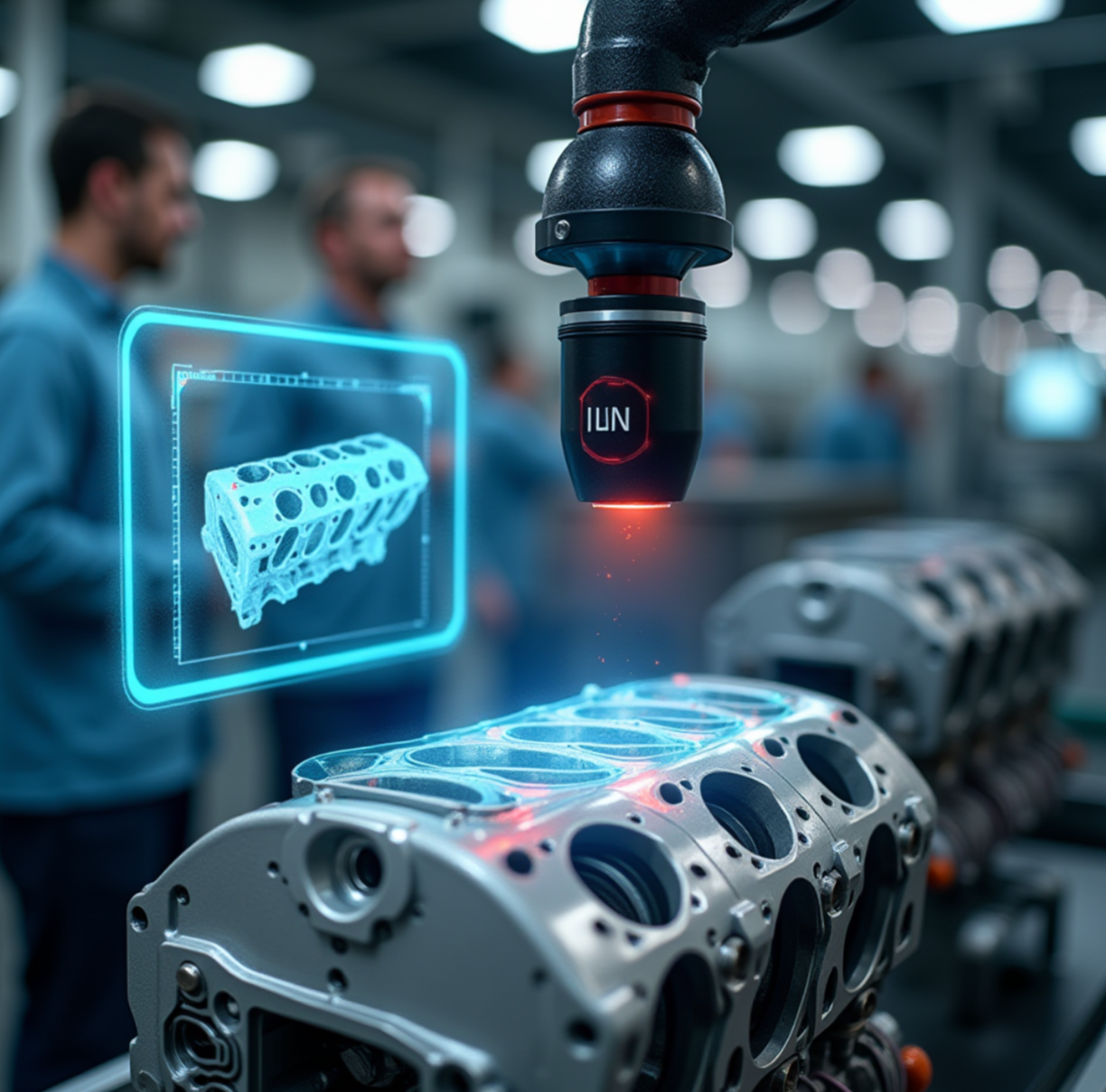
汽车制造检测图
电子制造:检测芯片焊接质量、电子元件的外观缺陷、印刷电路板(PCB)的线路完整性等。
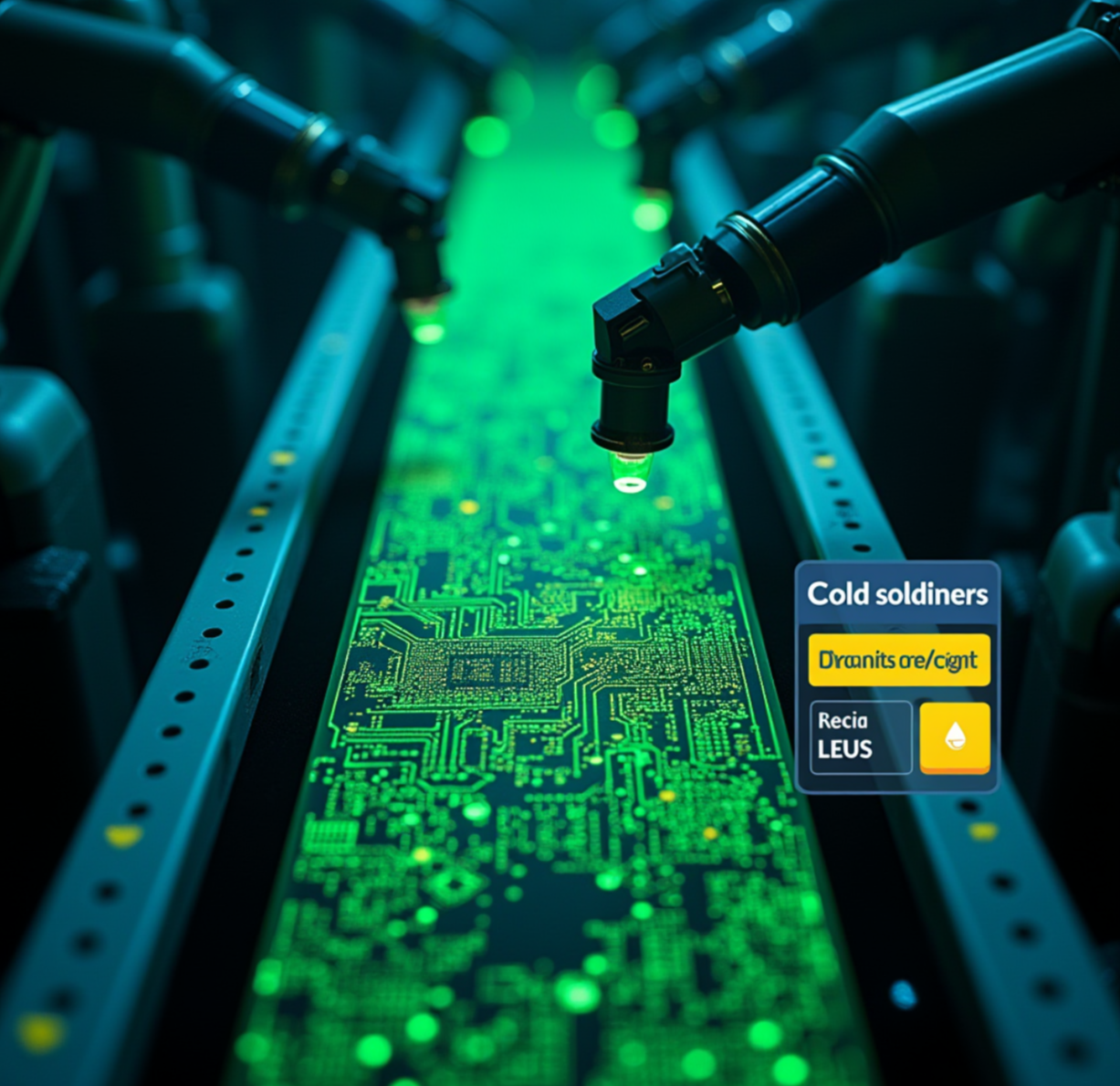
电子制造芯片检测图
食品饮料行业:检查包装标签的正确性、有效期信息的完整性、产品外观的缺陷等。
化工、化妆品和个人护理行业:确保产品包装和标签的正确性,检测产品外观的瑕疵等。
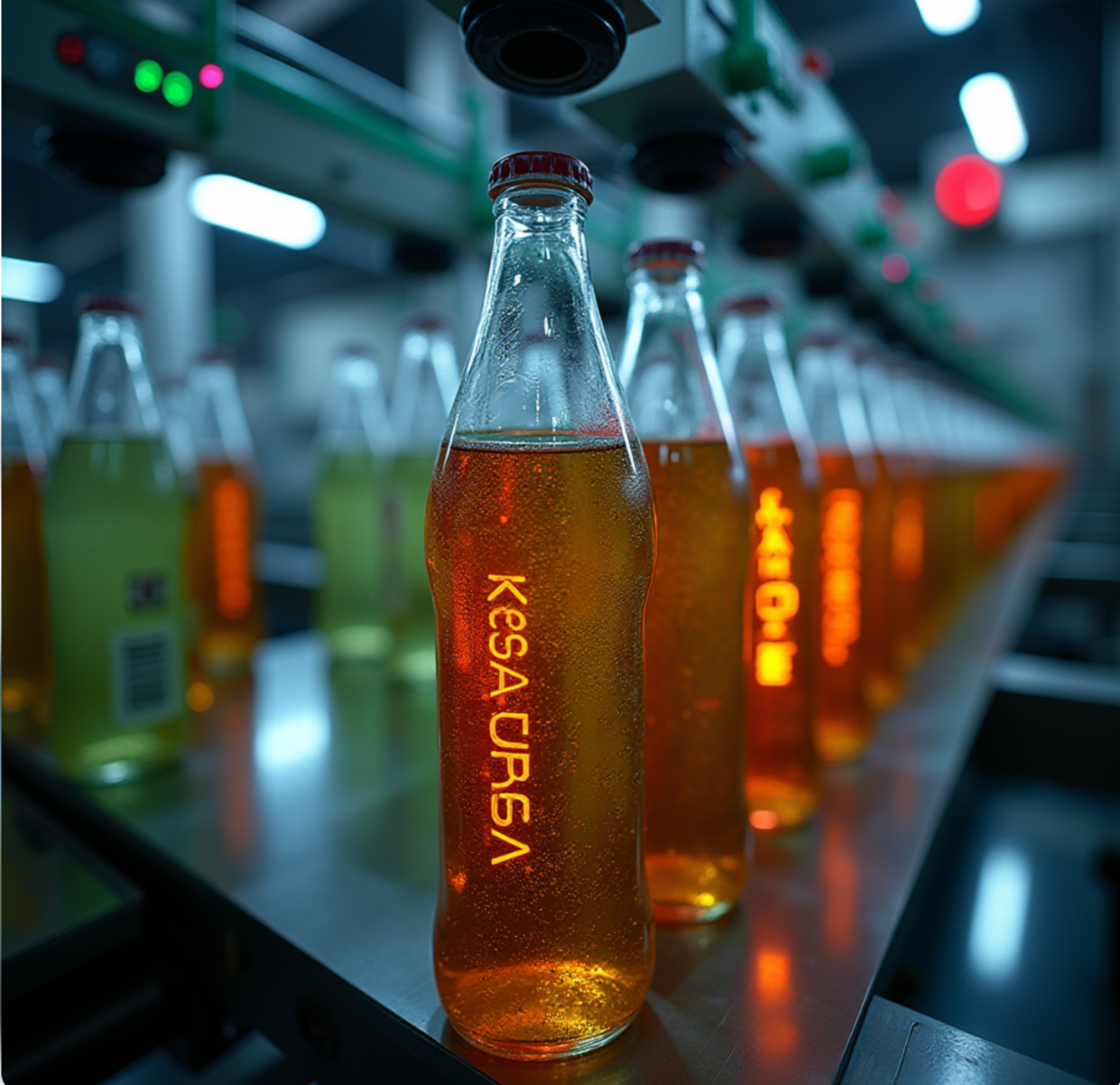
检测包装外观图
机械加工行业:检测零部件的尺寸精度、表面粗糙度、形状偏差等。
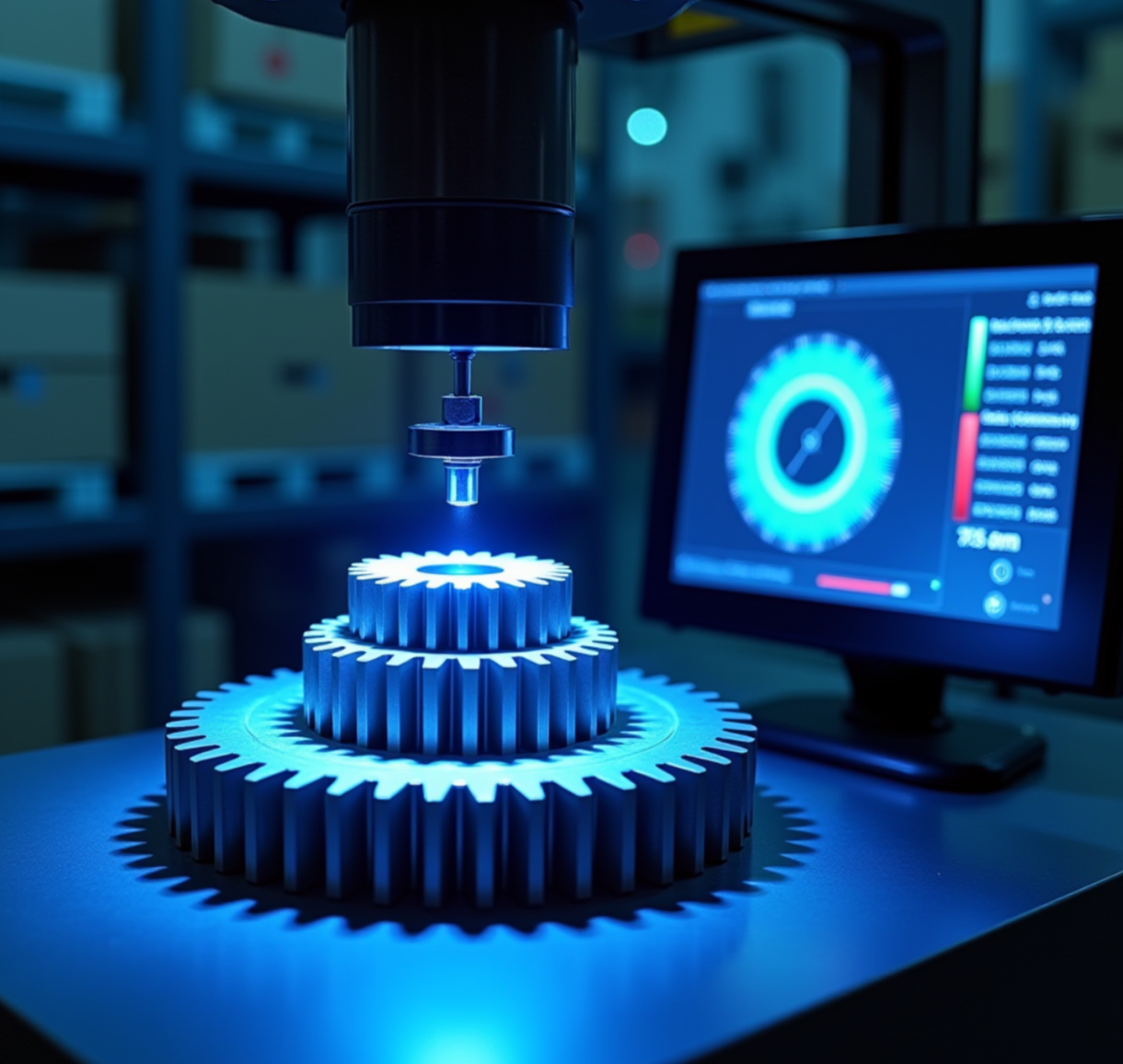
机械加工图
二、项目方向
本项目旨在通过先进的视觉检测技术,实现制造业生产过程中的自动化质量控制,提高检测效率和准确性,降低人工成本和误检率。具体目标包括:
实时缺陷检测:即时识别产品表面的划痕、凹陷、裂纹、孔洞等缺陷。
尺寸测量:精确测量零部件的尺寸,确保符合设计要求,公差控制在微米级别。
材料缺陷检测:检测材料表面的斑状、块状缺陷以及黑点、白点等小缺陷,适用于各种材质的检测。
组装质量控制:判断零部件的安装位置和精度,确保组装质量的一致性。
数据分析与优化:通过对检测数据的积累和分析,为企业提供质量改进的指导和决策依据,实现生产过程的持续优化。
三、项目技术流程
(一)设计方案
阶段 | 关键步骤 | 具体内容 |
需求分析 | 客户沟通 | 了解生产流程、质量控制标准、检测需求和预算。 |
产品特点分析 | 分析材质、形状、尺寸、表面处理工艺,确定检测项目及精度要求。 |
生产环境评估 | 考虑光照、温度、湿度等条件,确保系统稳定运行。 |
自动化水平评估 | 评估客户现有设备及管理系统,确定视觉检测系统的集成方式。 |
设备选型 | 工业相机 | 高精度测量:500万像素以上;快速产线:帧率≥100fps。 |
光源 | 反光材质:偏振光光源;透明材料:背光光源。 |
图像处理软件 | 需支持图像预处理、特征提取、缺陷识别、尺寸测量及机器学习算法。 |
机械控制模块 | 根据产线自动化程度选择机械结构和控制模块,确保与生产线同步运行。 |
系统集成 | 硬件集成 | 安装相机、光源、计算机等设备,确保覆盖检测区域且避免干扰;完成电气连接与机械固定。 |
软件集成 | 图像处理软件与自动化控制系统(如PLC)集成,实现检测数据实时传输和反馈。 |
接口开发 | 开发人机交互界面,功能包括:参数设置、结果查看、系统维护、故障诊断;支持数据存储、导出及追溯。 |
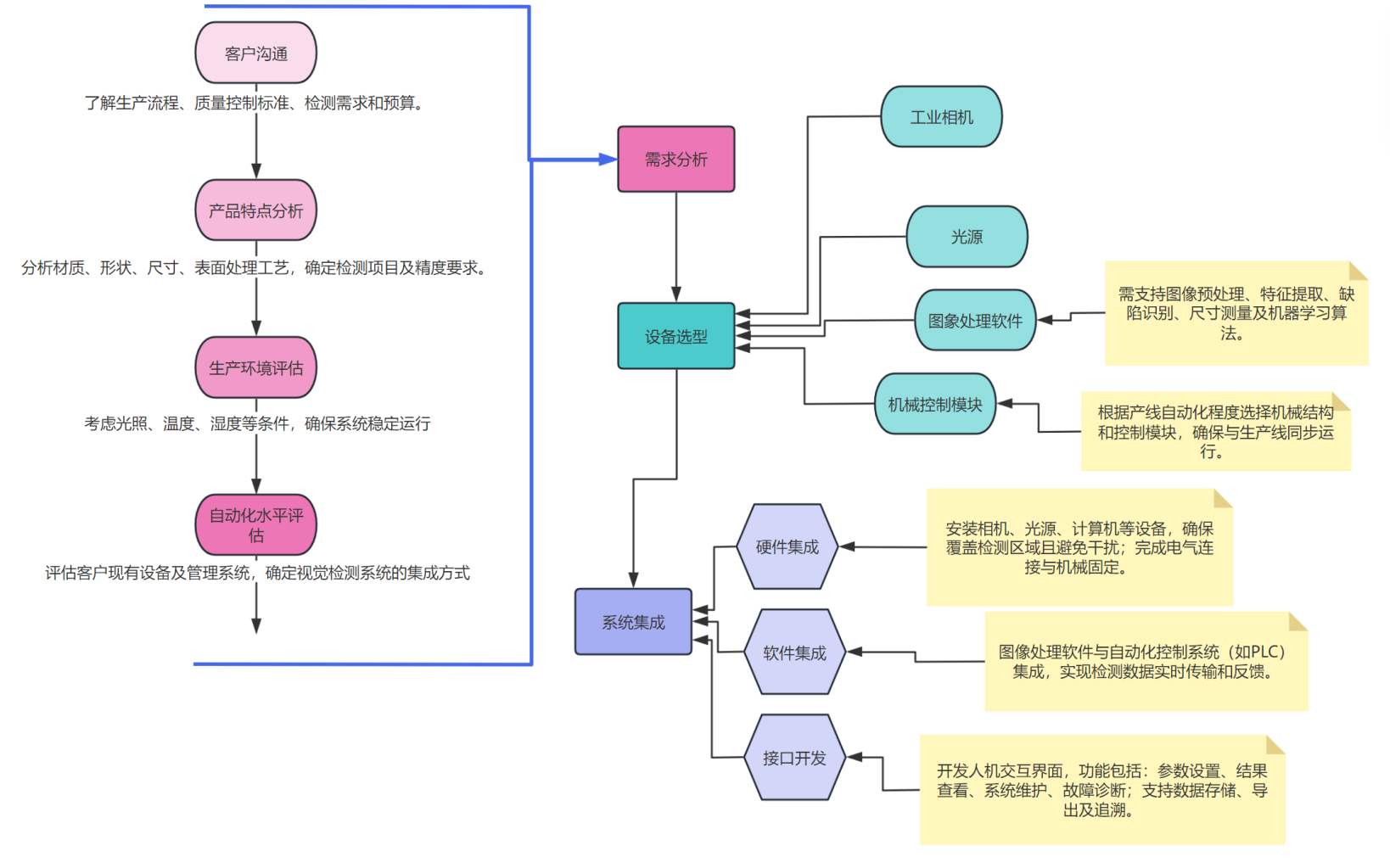
(二)架构设计
硬件架构
模块名称 | 核心组件 | 功能描述 |
图像采集模块 | 高分辨率工业相机、多光谱光源 | 相机:根据检测精度(如微米级)、速度(如100fps)及产品尺寸选择型号。 光源:针对材质(如反光/透明)定制波长和角度,确保图像清晰度与对比度。 |
数据处理模块 | AI图像处理软件(含深度学习算法) | 实时处理图像,完成预处理(降噪、增强)、特征提取、缺陷识别(如划痕、变形)。 需高性能GPU支持,计算延迟≤50ms,结果实时反馈至控制系统。 |
机械控制模块 | 机械传动装置、定位装置、驱动装置 | 同步生产线速度(如0.5m/s),精确控制检测设备运动(定位精度±0.1mm)。 包含伺服电机、导轨等,适应振动、粉尘等工业环境。 |
人机交互模块 | 图形化操作界面、数据接口 | - 界面功能:参数设置(如检测阈值)、实时结果展示(含NG标记)、历史查询。 - 数据交互:支持JSON/Excel格式输出,兼容MES/PLC系统,提供API接口。 |
软件架构
层级 | 功能描述 |
数据采集层 | 负责从图像采集模块获取原始图像数据,并进行初步图像预处理,如去噪、增强对比度等,以提高图像质量,为后续的处理和分析提供更好的基础。 |
数据处理层 | 运用机器学习和深度学习算法对图像进行处理和分析。该层包括特征提取、缺陷识别、尺寸测量等多个子模块,能够自动识别图像中的缺陷、测量产品的尺寸,并判断是否符合质量标准。 |
数据分析层 | 对检测结果进行统计分析,生成质量报告,并提供优化建议。该层能够对大量检测数据进行分类、汇总和分析,找出质量控制的关键点和薄弱环节,为企业提供决策支持。 |
应用层 | 实现与生产线的自动化控制系统和企业资源规划(ERP)系统的数据交互。该层通过标准的通信协议和接口,将检测结果实时反馈到生产管理系统,以便及时调整生产过程;同时,将数据上传到ERP系统,实现质量数据的集中管理和追溯。 |
四、技术方案
高精度图像采集:
技术环节 | 具体实施方案 |
相机选型 | 采用高性能CMOS工业相机,分辨率500万像素以上,帧率100fps以上,支持全局快门和高速数据传输接口,确保在快速移动的生产线上仍能获取清晰、无拖影的图像 |
光源设计 | 根据检测物材质特性配置多光谱光源系统,包含环形光、同轴光、背光等多种照明方式,采用可编程控制器精确调节光强(0-100%可调)和照射角度(0-90°可调),有效消除金属反光、透明材质折射等干扰 |
图像预处理 | 采用多级处理流程: 1. 自适应中值滤波消除随机噪声 2. 基于Retinex理论的非均匀光照补偿 3. 多尺度边缘增强算法 4. 局部对比度受限直方图均衡化(CLAHE) |
AI驱动的图像处理
技术要点 | 详细说明 |
深度学习算法 | 采用CNN、YOLO等算法(如YOLO11模型),实时识别缺陷并支持多类型扩展。 |
特征提取与匹配 | 提取边缘/形状/纹理特征,与标准模板匹配(如轮廓尺寸对比公差范围)。 |
缺陷分类与识别 | 划分划痕/凹陷/裂纹等类型,评估大小/位置/形状以判定质量影响程度。 |
实时反馈与自动化控制:
数据传输与反馈:检测结果通过高速通信接口实时反馈到生产管理系统,如PLC、MES(制造执行系统)等,以便及时调整生产过程。例如,当检测到产品存在缺陷时,系统可立即发出警报,并将该产品标记为不合格品,同时调整生产线的速度或暂停生产,以便进行后续的处理。
自动化控制与调整:与生产线的自动化控制系统进行无缝集成,实现自动化的质量控制和生产流程优化。例如,根据检测结果,自动调整生产设备的参数,如加工速度、切削深度等,以提高产品质量的一致性;同时,通过自动化控制系统,实现检测设备的自动校准和维护,确保检测结果的准确性。
数据分析与优化
技术要点 | 详细说明 |
质量数据统计与分析 | 计算缺陷率/合格率,识别异常批次或设备,定位质量薄弱环节。 |
趋势分析与预测 | 分析缺陷率时序变化,预测设备老化/工艺漂移,触发预防性维护。 |
工艺优化建议 | 调整温度/压力/时间等参数,优化生产布局以降低缺陷率。 |
质量改进闭环 | 数据反馈至生产流程,持续优化实现智能化制造。 |